Как делают керамическую посуду на заводе
Керамическая посуда, кажется, никогда не выйдет из моды. Какие бы новые технологичные материалы не появлялись на кухне, керамика все равно остается одним из самых распространенных видов сырья для производства посуды и домашней утвари. Почему – тема для отдельного разговора. А сегодня я предлагаю ответить на другой вопрос: как делают керамическую посуду сейчас, спустя тысячелетия после изобретения материала.
Содержание:
- Кратко: технологии производства керамической посуды
- Как делают посуду из керамики методом шликерного литья
Кратко: технологии производства керамической посуды
Сейчас существует несколько базовых технологий изготовления керамической посуды. Ключевая разница между ними – процесс формовки основы из глиняной заготовки, который, в свою очередь зависит от нескольких факторов. Например, доступного оборудования на производстве или необходимых объемов. То есть, конечно, можно вылепить все изделия на гончарном круге, но действительно крупный завод едва ли будет использовать этот техпроцесс, предпочтя вместо него что-то более производительное и масштабное. В общем, предлагаю остановиться на каждом варианте подробнее.
Свободная лепка
Тут все просто и понятно практически без дополнительных объяснений: изделия лепят полностью вручную из глины, по консистенции напоминающей пластилин. Для проработки сложных деталей могут использовать дополнительный инструмент, например, деревянные или металлические стеки или штампы, которые позволяют формировать объемный узор из повторяющихся элементов.
В керамической посуде ручной работы есть свой шарм: толстые стенки, не всегда ровные линии и неповторимость каждого изделия. Но для промышленного, массового производства такой вариант не подходит: слишком малые объемы, большие затраты времени и сил на одно изделие и очень плохая повторяемость – изготовить целую партию одинаковых изделий (например, сервиз) сложно.
Формовка на гончарном круге
Здесь ситуация во многом похожа на ручную формовку, но для удобства используется гончарный круг. В большинстве своем, электрический. Глину накладывают на него горкой, а затем формируют во время вращения руками или дополнительными инструментами – плоскими, зубчатыми или петельчатыми стеками.
Таким способом удается получить гораздо более ровную посуду, с относительно тонкими и гладкими стенками без следов пальцев. Однако, во-первых, такой способ плохо подходит для изготовления плоских тарелочек и блюд. Во-вторых, «масштабность» у него примерно как у ручной лепки. То есть, на больших заводах такой метод едва ли используют. Однако частные гончарные мастерские вполне могут работать на поток именно по такой технологии. Изделия в этом случае также получаются ручной работы (с присущими ей «шероховатостями» и более высокой ценой), но объемы производства увеличить проще.
К слову, у этой и предыдущей технологии есть еще один большой минус: человеческий фактор. Крупные заводы в любой индустрии стремятся свести его влияние на продукцию к минимуму. То есть, производственный процесс должен быть устроен таким образом, чтобы качество производимой продукции минимально зависело от опыта сотрудников. Здесь же все наоборот: итоговая красота и качество посуды зависят исключительно от рук мастера. И чтобы увеличить производительность, нужно либо упрощать изделие, либо вкладывать силы и время в обучение новых мастеров.
Ручной оттиск
В этом случае вместо формовки заготовки руками ее закладывают в предварительно подготовленную форму, а затем прижимают. Форма может быть плоской или разъемной.
Эта технология хоть и позволяет нарастить темп и увеличить повторяемость, так как из формы выходят абсолютно одинаковые изделия, но непосредственно для производства посуды используется нечасто. В лучшем случае, для отдельных элементов, например, декоративных накладных деталей вроде листочков или цветов на кружках или чайниках.
Формирование во вращающейся форме
Этот метод является своеобразным сочетанием гончарного круга и ручного оттиска, поскольку здесь используется полая вращающаяся форма, в которую закладывается глина. Форма изготавливается из гипса и имеет разъемную конструкцию. Помещенная внутрь глиняная масса распределяется с помощью формующего шаблона или ролика. Количество глины при этом рассчитывается по объему готового изделия. После распределения материала форму снимают с вращающегося стола и отправляют на сушку. После высыхания ее раскрывают, а получившуюся заготовку отправляют на доработку, например, крепление дополнительных элементов.
Как и в случае с гончарным кругом, таким способом удобнее всего производить объемные пустотелые изделия, например, горшочки, вазы или основы для чайников. Однако для тарелок он не подходит. Зато таким способом можно добиться достаточно большого объема производства и хорошей повторяемости.
Шликерное литье
Пожалуй, самый популярный метод на современных заводах. Его суть в том, что в гипсовую разъемную форму не закладывается, а заливается жидкий керамический состав. Таким способом можно производить изделия практически любой формы, в том числе, с красивыми фактурными стенками. Подробнее о том, как устроен процесс, я расскажу отдельно, далее по тексту.
Комбинированный метод
Как несложно догадаться по названию, комбинированный метод предполагает использование сразу нескольких технологий. Особенно актуально это для изделий сложной формы. Например, чайников, кружек или моделей, украшенных накладными элементами вроде уже упомянутых мной цветов и листочков. В этом случае основа может, например, формироваться на гончарном круге, а накладные элементы – ручным оттиском в форме. А после того, как отдельные детали достаточно подсохнут, их собирают в готовое изделие. Уже после этого оно окончательно сушится, оформляется и запекается.
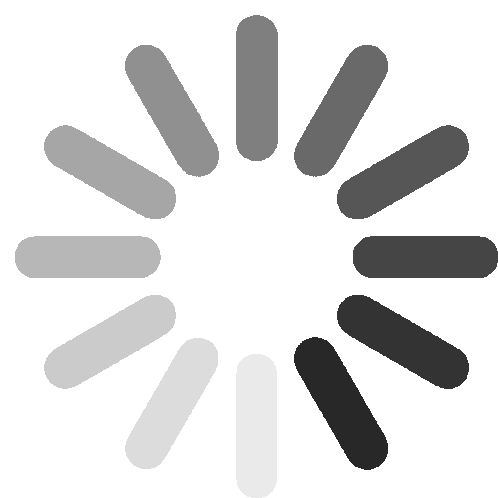
Как делают посуду из керамики методом шликерного литья
Шликерное литье – один из самых распространенных методов изготовления керамической посуды, особенно для изделий сложной формы. Он позволяет создавать тонкостенные и изящные изделия, которые сложно или невозможно сделать вручную или на гончарном круге. Процесс состоит из серии стандартных этапов.
- Подготовка шликера. Шликер – это жидкая керамическая масса, которая используется для литья в формы. Изначально она представляет собой сухую порошкообразную смесь из глины с разными добавками, призванными предотвратить слипание частиц и улучшить текучесть массы. Для работы порошок замешивается с водой до однородной консистенции, чтобы избежать комков и пузырьков воздуха
- Изготовление гипсовой формы. Форма – ключевой элемент шликерного литья. Ее изготавливают на основе мастер-модели (она также может быть глиняной или пластиковой, отпечатанной на 3D-принтере) из гипса. В большинстве случаев она состоит из двух половин, но если у изделия по-настоящему сложный дизайн, частей может быть и больше.
- Заливка шликера в форму. В форме оставляют специальное отверстие, через которое и заливают шликер. И поскольку гипсовое основание – пористое, оно начинает впитывать воду, а внутри формы остается более плотная глиняная масса.
- Выдержка. Итоговое время выдержки зависит от свойств самого шликера и толщины стенок изделия – чем дольше шликер находится в форме, тем толще будут стенки. В среднем этот этап занимает от нескольких минут до получаса.
- Слив излишков шликера. После того, как на стенках формы образовался достаточный слой керамики, оставшийся шликер сливают.
- Сушка в форме. Изделие оставляют в форме для дополнительной сушки. Гипс продолжает впитывать влагу, что делает керамику более твердой. После сушки изделие аккуратно извлекают из формы, разъединяя ее на несколько частей.
- Доработка изделия. После извлечения из формы изделие может иметь швы от затекшего между половинками состава, неровности, а также литник от отверстия. Их удаляют с помощью жесткой губки, ножа или наждачной бумаги. Также на этом этапе в конструкцию добавляют мелкие детали вроде ручек, носиков или декора, если они не были отлиты вместе с основным изделием. Их могут производить другими методами или также отливать, но в отдельных формах. Причем на крупных производствах мелкие детали отливают сразу партиями, по несколько штук в одной форме.
- Обжиг. Изделие сушат до полного удаления влаги, а затем обжигают в печи при высокой температуре. Температура обжига зависит от состава глины. Чаще всего используют температурный диапазон 900–1300°C. Это только первый обжиг (так называемый «утильный»). Он делает глину прочной, но при этом она остается пористой, а значит, боится воды. Эту проблему устраняют на следующем этапе.
- Глазурование. Собственно, керамические изделия отличаются от глиняных именно наличием глазури – стекловидного покрытия, которое делает поверхность водонепроницаемой, а также дополнительно повышает общую прочность. То есть, оно выступает эдаким «панцирем». Кроме того глазурь сама по себе влияет на красоту изделия – оно становится гладким и блестящим. Закрепляют глазурь вторым обжигом. Его также зависит от состава глазури, а также от используемого материала основы. Например, для производства фаянса – относительно мягкого, крупнопористого материала, используют низкотемпературный обжиг – 960-1080°С (иногда до 1280°), а для твердого фарфора с тонкими (менее 3 мм) стенками – высокотемпературный – 1350°С и более.
- Декорирование. На этом этапе изделие украшают. Тут достаточно много вариантов – от однотонной цветной глазури и ручной росписи до трафаретной или УФ-печати. В зависимости от используемой техники, может потребоваться третий и последний обжиг, который закрепит рисунок на поверхности эмали.
Напоследок отмечу, что, несмотря на ряд внушительных преимуществ вроде возможности производства очень сложных изделий (причем не только посуды, но и статуэток и скульптур), у шликерного литья есть и ощутимые недостатки. Например, необходимость предварительного изготовления форм и их периодической замены из-за износа, а также достаточная трудоемкость процесса. Особенно, если сравнивать с ручной лепкой или работой на гончарном круге. Но. Тем не менее, большинство производителей используют на своих заводах для изготовления керамической посуды именно его.